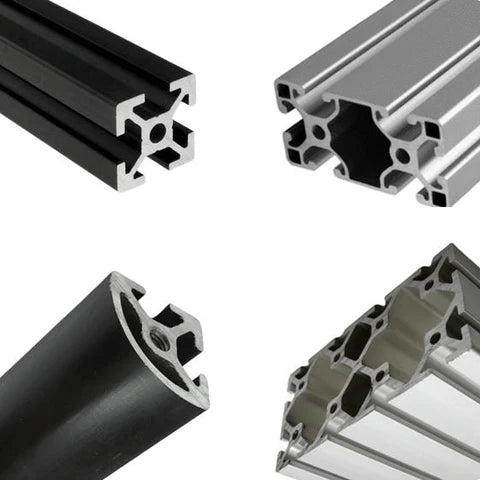
Aluminum Extrusions
At Forces, our smooth t-slotted aluminum extrusions are known for their strength, versatility, and lightweight properties, making them ideal for a wide array of applications. Make sure to check all of our different series (10, 15, 20, 30 or 40) depending on your specific needs.
10 Series Aluminum Extrusions (1" x 1")







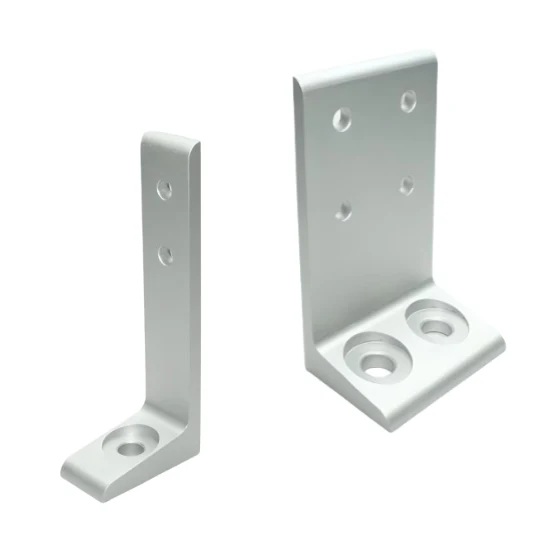


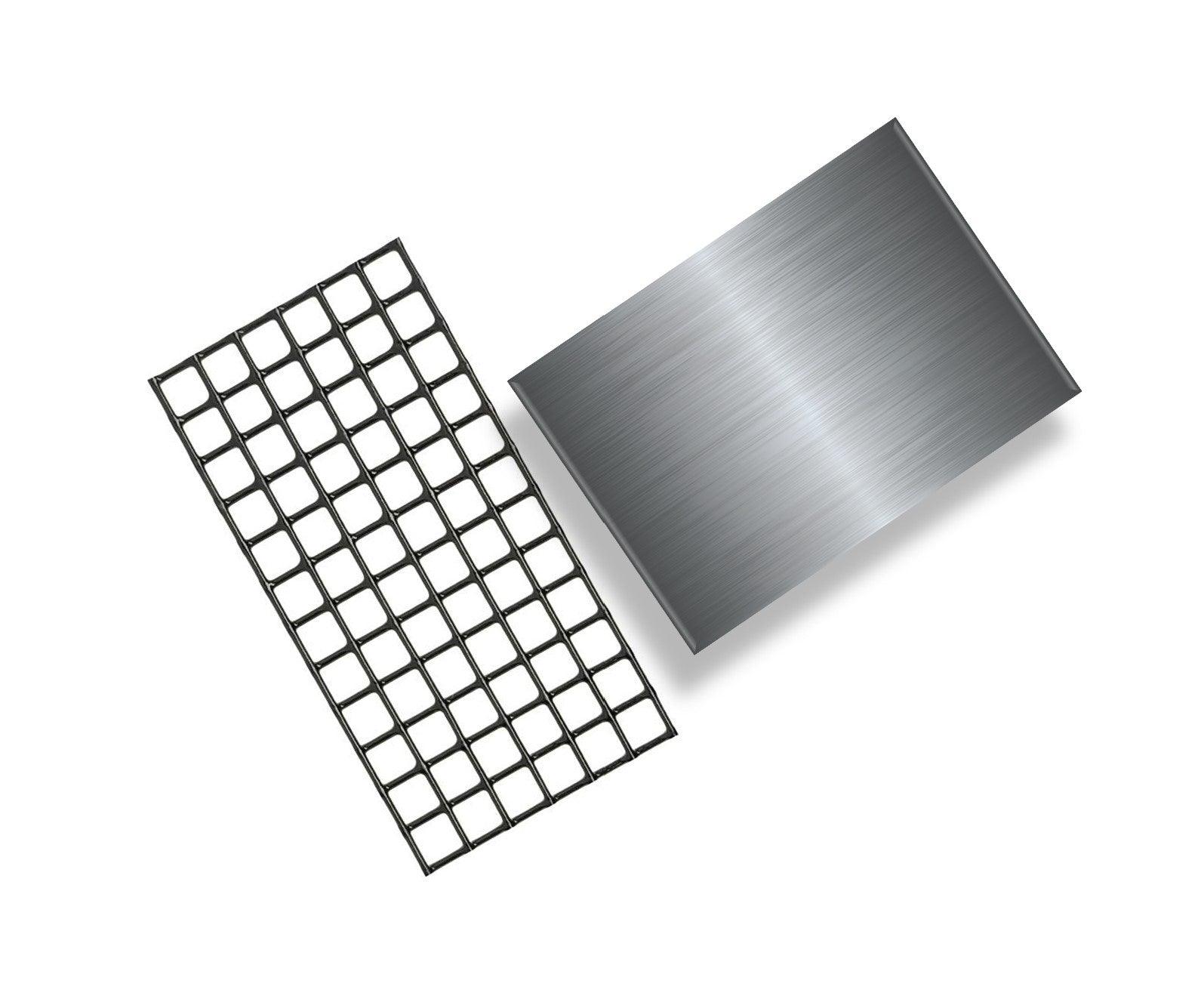
15 Series Smooth T-Slotted Aluminum Extrusions (1.5" x 1.5")










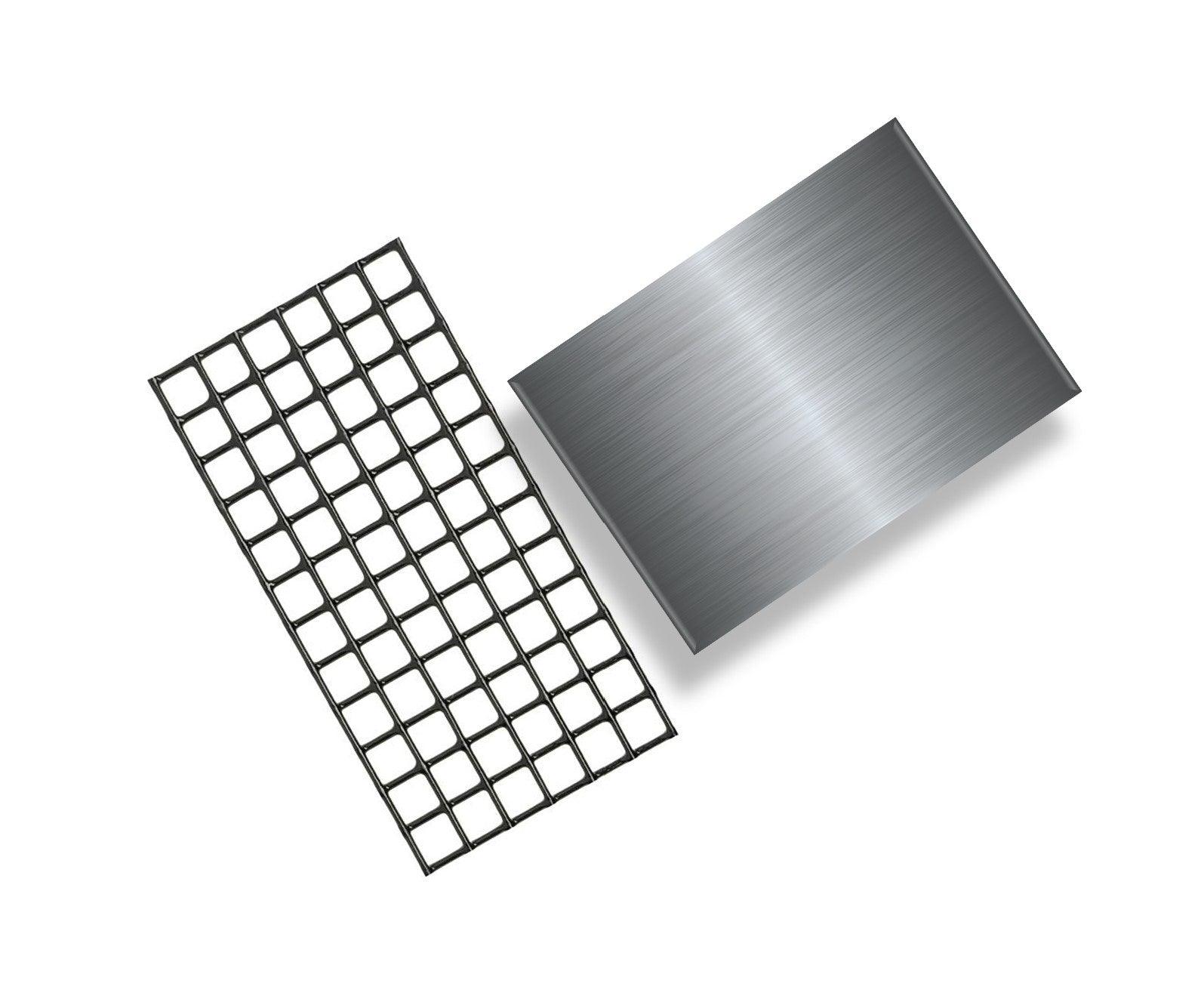
20 Series Aluminum Extrusions (20mm x 20mm)
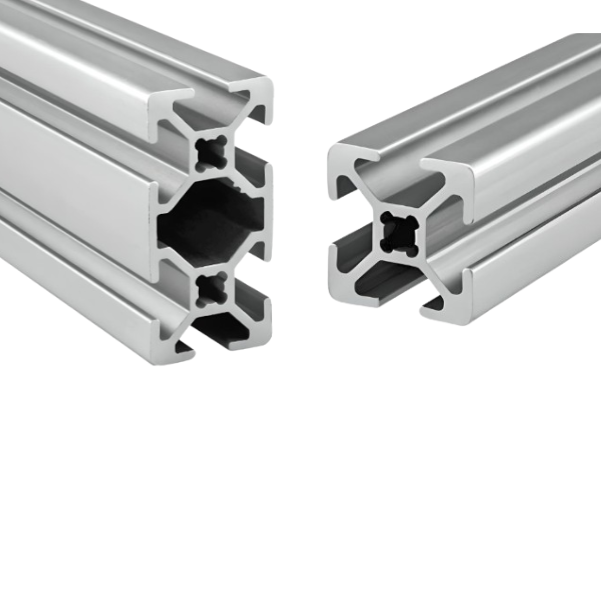
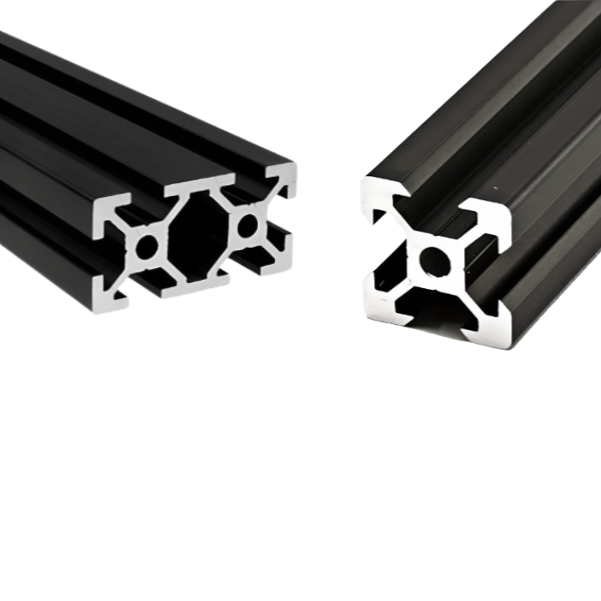
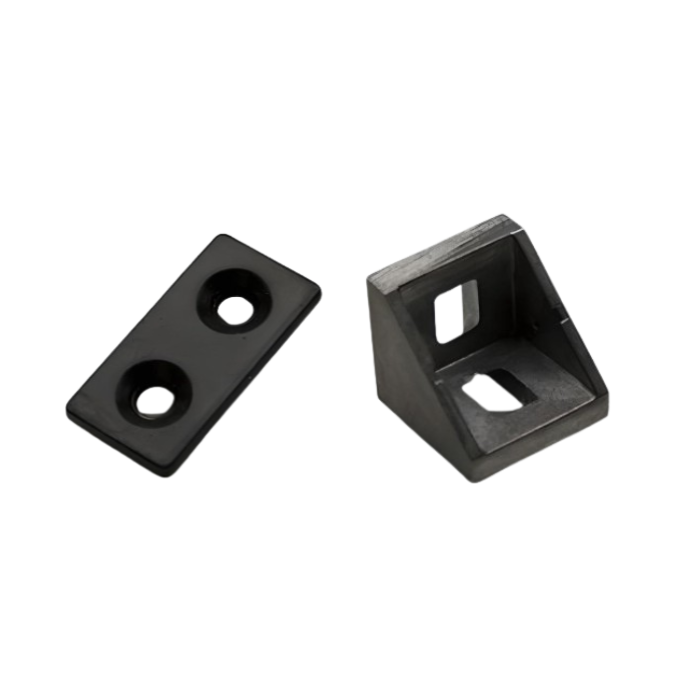

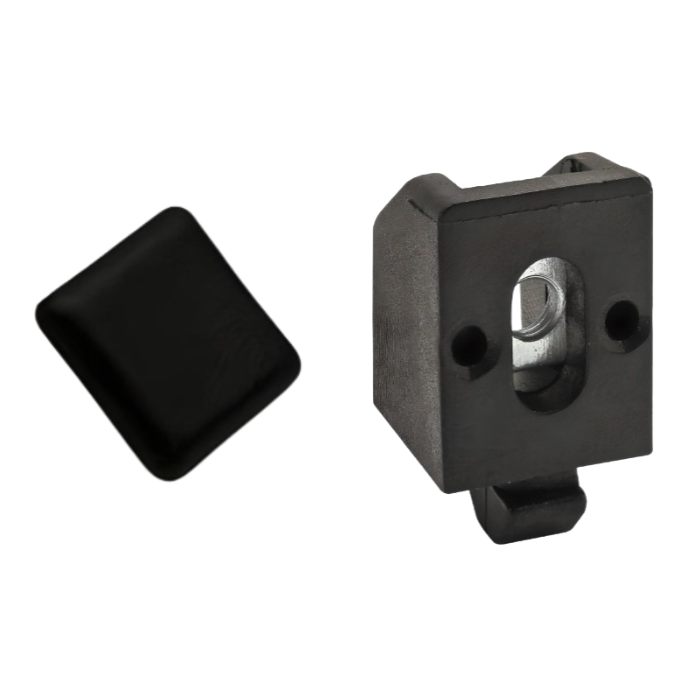
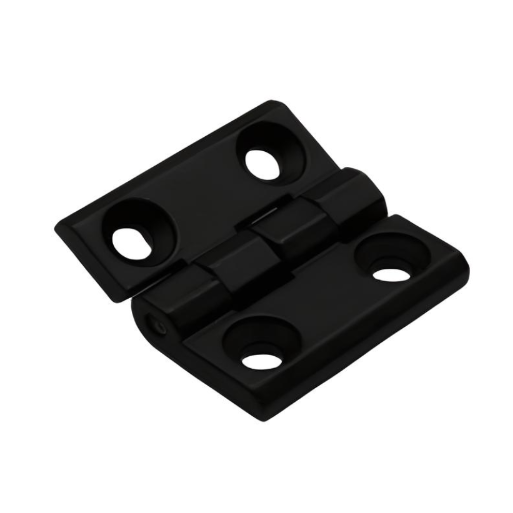
30 Series Aluminum Extrusions (30mm x 30mm)


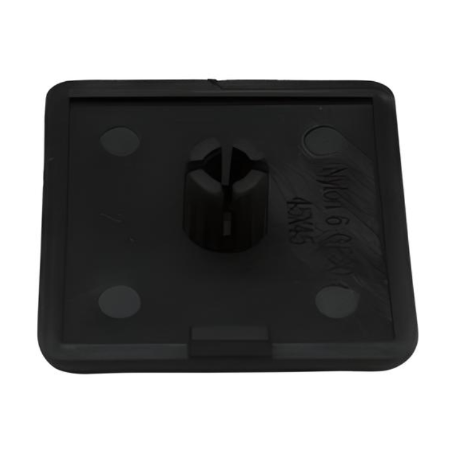

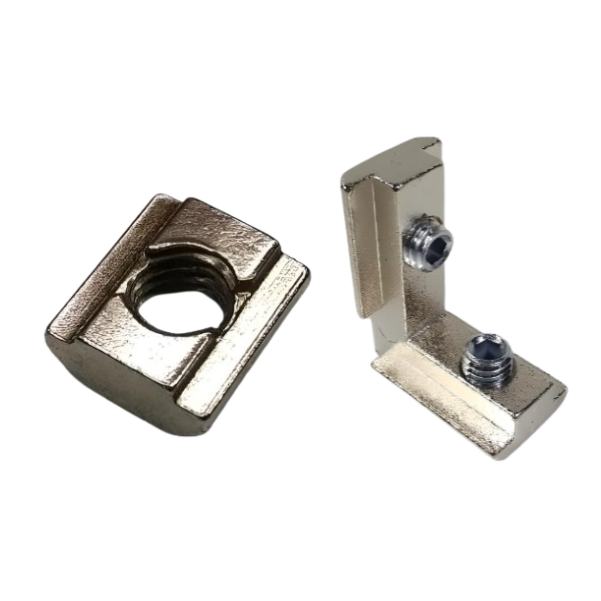
45 Series Aluminum Extrusions (45mm x 45mm)


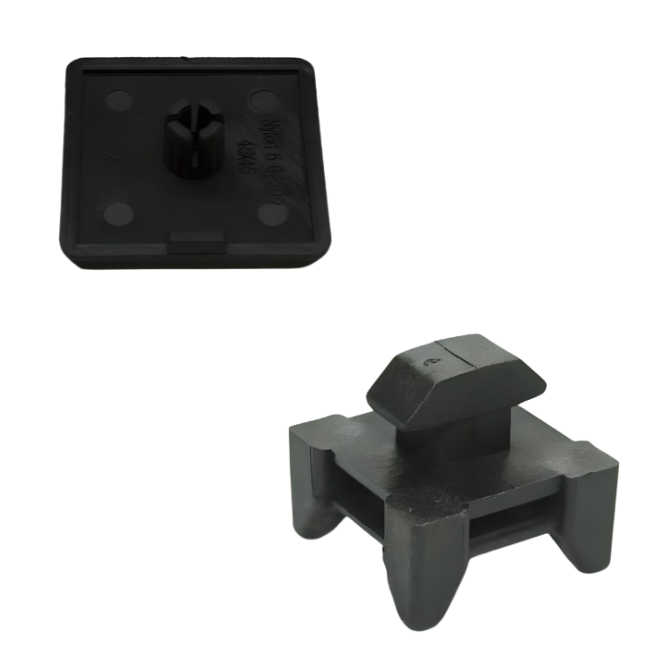
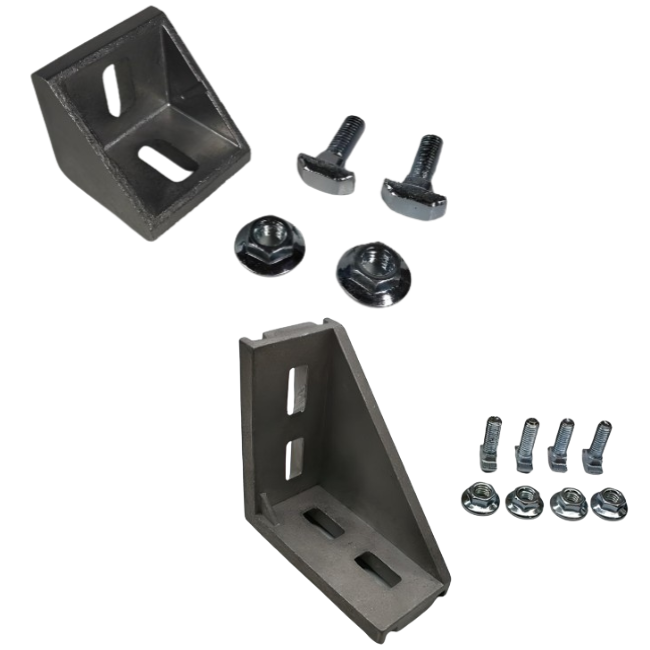

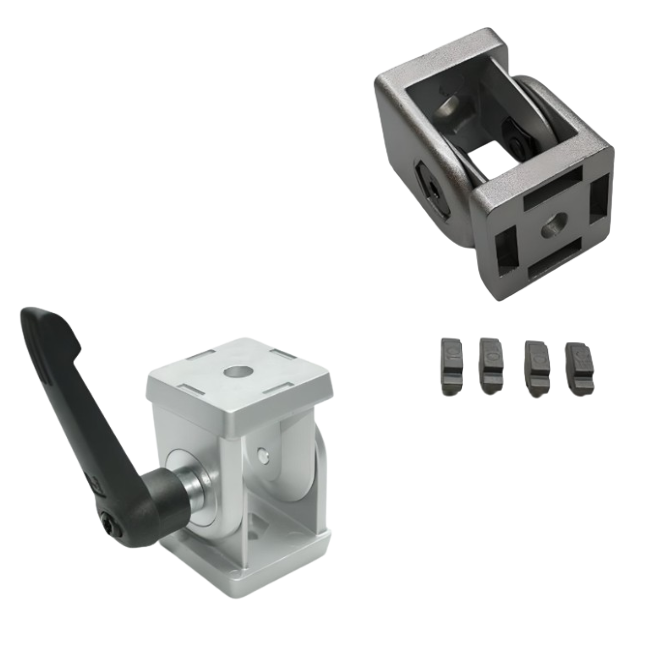
FAQ
Aluminum extrusions are products formed by forcing aluminum alloy material through a shaped die to create specific cross-sectional profiles. This process, known as extrusion, allows for the production of complex shapes with high precision and consistency. Aluminum extrusions are widely used in various industries due to their excellent mechanical properties, including strength, durability, and corrosion resistance.
Aluminum extrusions are used in a wide range of applications across multiple industries. Some common uses include:
- Construction: Used in framing, window and door profiles, curtain walls, and structural components.
- Manufacturing: Used in machinery, equipment, and assembly lines for various structural and functional purposes.
- Consumer Products: Found in furniture, appliances, electronics, and sporting goods due to their versatility and aesthetic appeal.
Their ability to be customized into complex shapes and sizes makes aluminum extrusions essential in many applications.
Aluminum extrusions are made through a process that involves several key steps to ensure precision and quality:
- Billet Preparation: Aluminum billets (cylindrical blocks) are heated to a specific temperature to make them malleable.
- Extrusion: The heated billet is forced through a die with the desired cross-sectional shape using a hydraulic press. This process shapes the aluminum into the specified profile.
- Cooling: The extruded aluminum is cooled rapidly to maintain its shape and structural integrity.
- Cutting: The extrusions are cut to the required lengths for further processing or finishing.
- Heat Treatment: The extrusions may undergo heat treatment to enhance their mechanical properties and strength.
- Finishing: Surface treatments such as anodizing, painting, or powder coating are applied to improve corrosion resistance and aesthetic appeal.
- Quality Control: Each extrusion is inspected and tested to ensure it meets industry standards and customer specifications.
This comprehensive process ensures that our aluminum extrusions provide high performance and reliability in various applications.
Aluminum extrusions offer numerous advantages that make them a preferred choice in many industries:
- Lightweight: Aluminum is significantly lighter than other metals, reducing the overall weight of structures and components.
- Strength: Despite being lightweight, aluminum extrusions offer excellent strength and can be designed to meet specific load-bearing requirements.
- Corrosion Resistance: Aluminum naturally forms a protective oxide layer, making it highly resistant to corrosion and ideal for outdoor and harsh environments.
- Versatility: The extrusion process allows for the creation of complex and custom shapes, providing flexibility in design and application.
- Sustainability: Aluminum is recyclable, making it an environmentally friendly material that can be reused without losing its properties.
- Aesthetic Appeal: Aluminum extrusions can be finished in various ways to enhance their appearance, making them suitable for both functional and decorative purposes.
These advantages make aluminum extrusions an ideal choice for a wide range of applications, providing both functional and economic benefits.