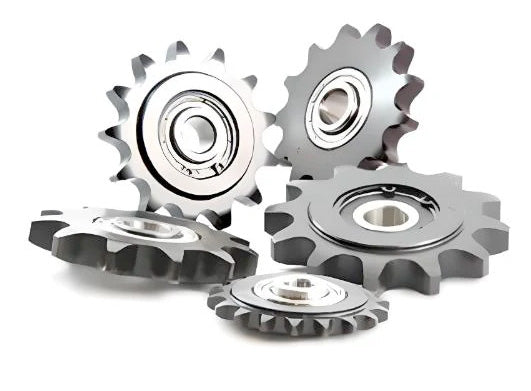
Sprocket
Our comprehensive selection of sprockets is designed to meet the needs of various industries and applications. Whether you require sprockets for machinery or for conveyors, we offer durable and high-performance solutions to keep your operations running smoothly.
Roller Chain Sprockets
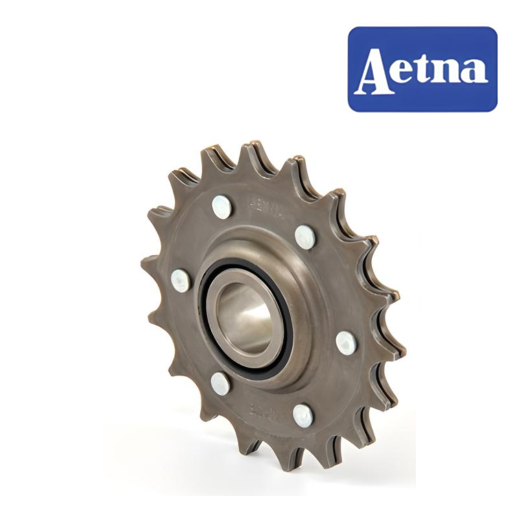
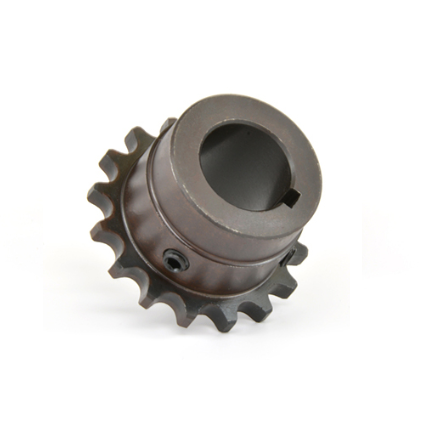
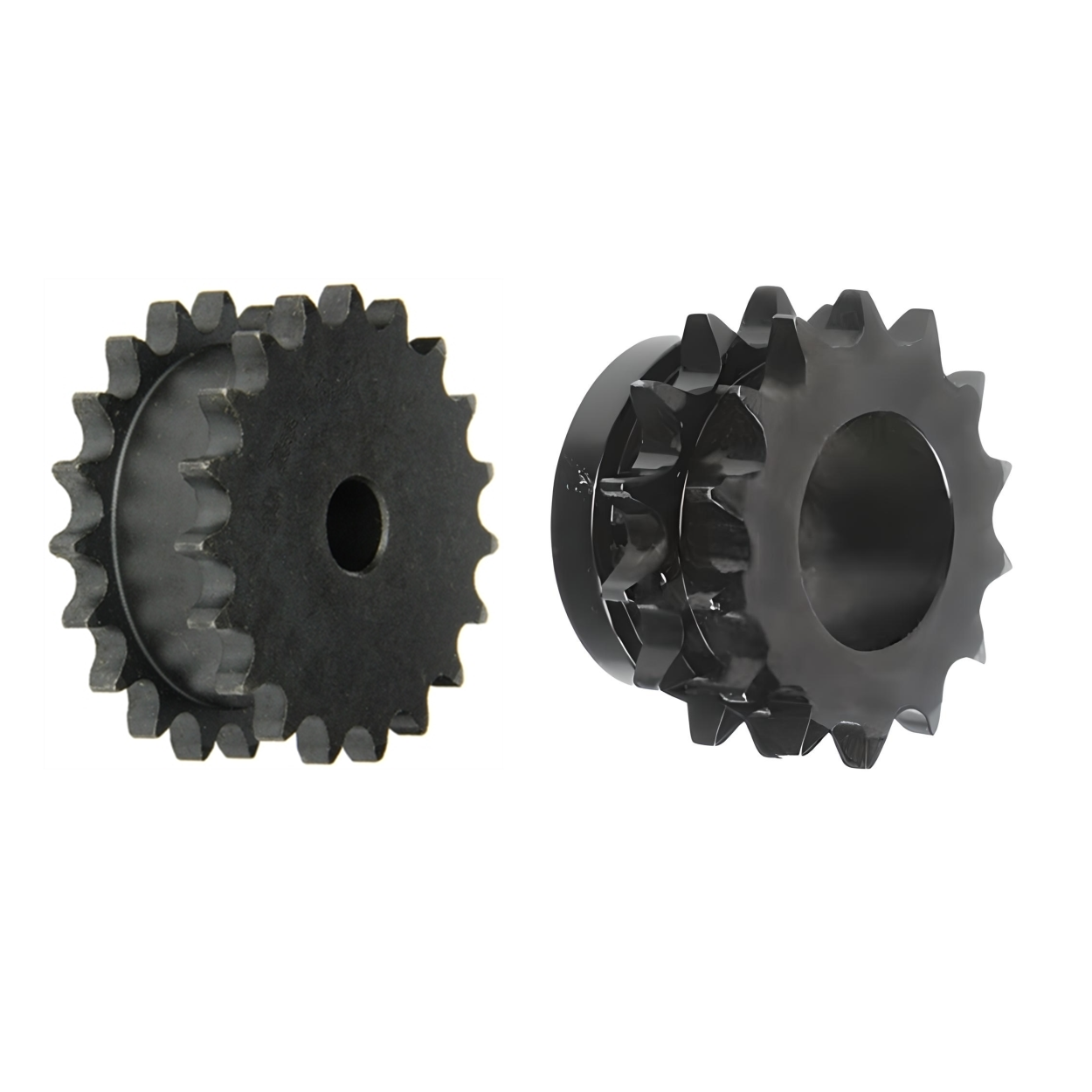

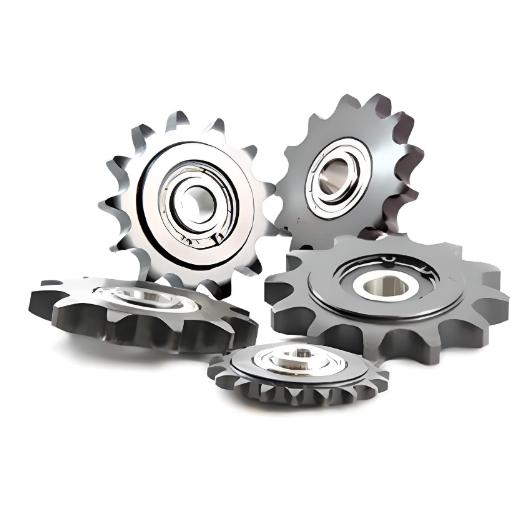
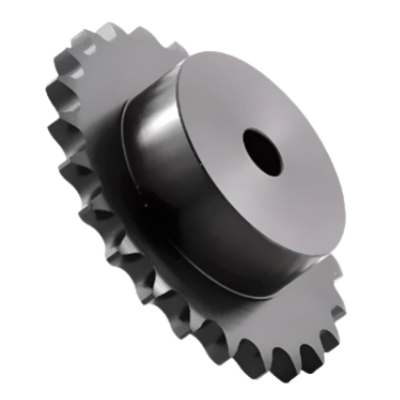
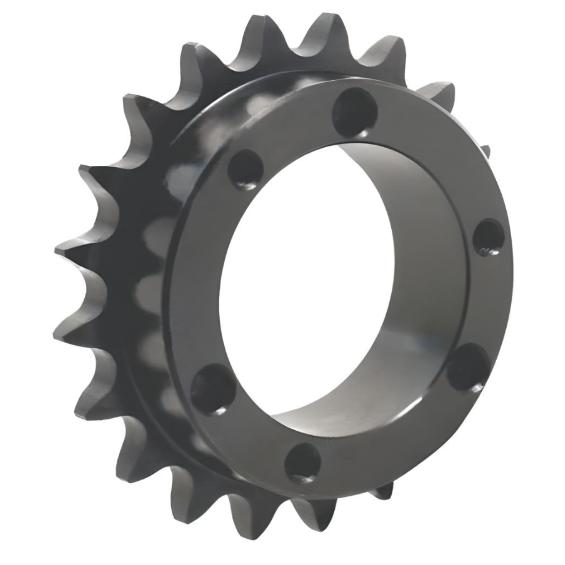
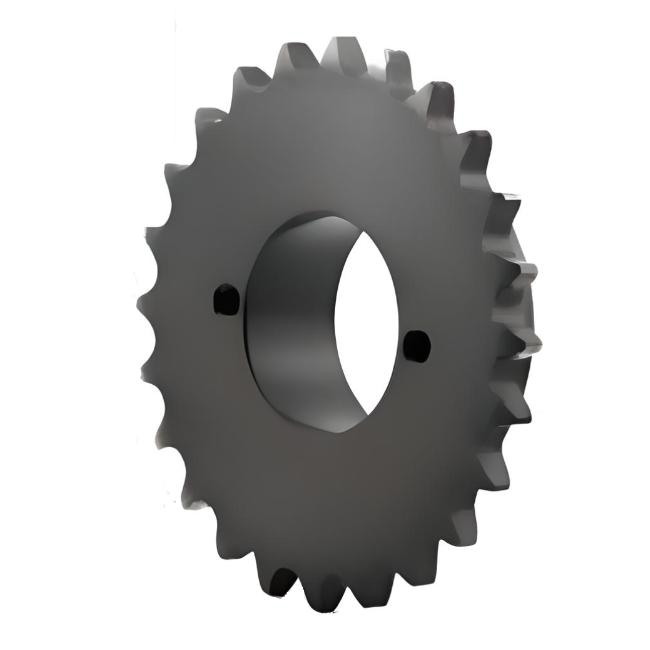
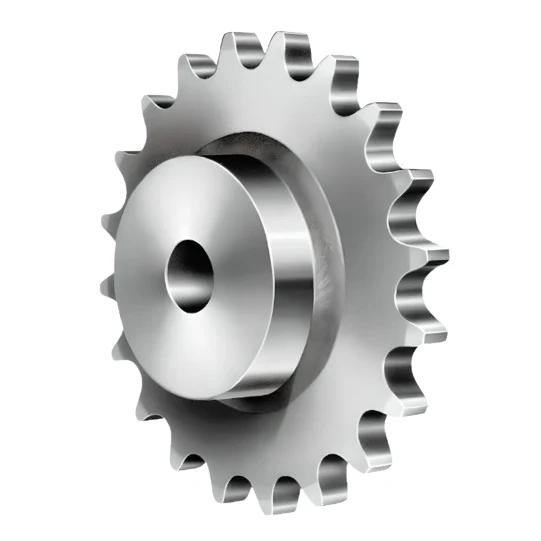

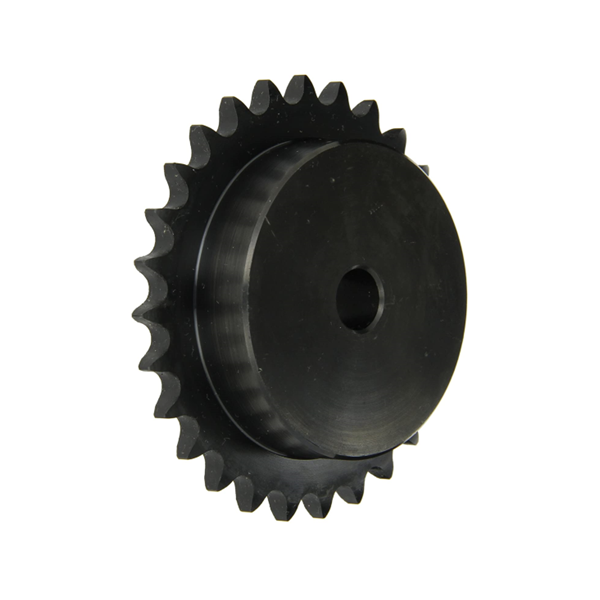
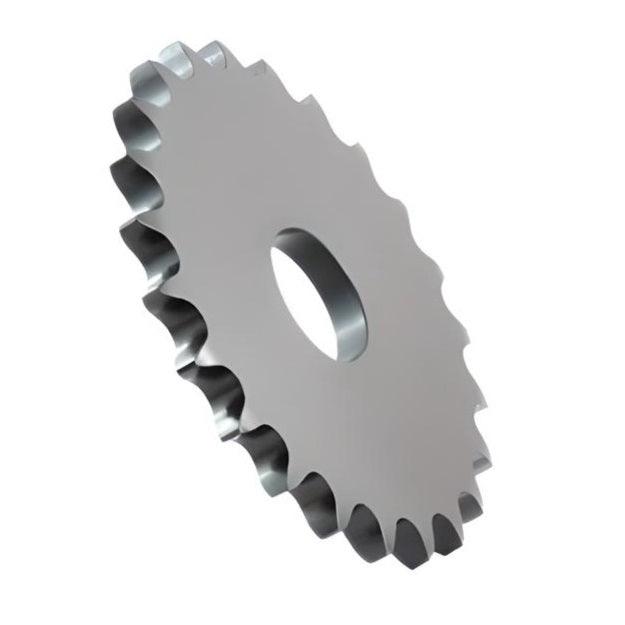
Frequently Asked Questions
Sprockets are mechanical devices with teeth or cogs that mesh with a chain, track, or other perforated or indented material. They are used to transmit rotary motion between two shafts where gears are unsuitable or to impart linear motion to a track, tape, or other flexible material. Sprockets are a crucial component in many mechanical systems, providing a reliable and efficient means of power transmission.
Sprockets are used in a wide range of applications due to their versatility and efficiency. Common uses include:
- Industrial Machinery: Sprockets are used in conveyor systems, milling machines, and material handling equipment to transfer power and motion.
- Automotive: They are found in motorcycles, bicycles, and automotive engines, providing a means to drive the chain and transfer power from the engine to the wheels.
- Agricultural Equipment: Sprockets are used in tractors, harvesters, and other farming machinery to facilitate various mechanical movements.
- Construction Machinery: They are employed in equipment like bulldozers and excavators to drive tracks and facilitate movement.
- Printing and Packaging: Sprockets help in the movement of paper, film, and packaging materials through various stages of production.
Their ability to provide precise and efficient power transmission makes sprockets indispensable in many industries.
Sprockets work by engaging with a chain or other perforated material to transfer rotary motion. Here’s a basic overview of their operation:
- Engagement: The teeth of the sprocket mesh with the links of the chain, ensuring a secure grip.
- Rotation: As the sprocket rotates, it pulls the chain along with it, converting the rotary motion of the sprocket into linear motion of the chain.
- Power Transmission: The motion is transferred from one sprocket to another, or from a sprocket to another mechanical component, enabling the transmission of power and motion.
- Efficiency: The precise meshing of the sprocket teeth with the chain links ensures minimal slippage and efficient power transfer.
This simple yet effective mechanism allows sprockets to deliver reliable performance in a variety of applications.
The manufacturing of sprockets involves several key steps to ensure durability and precision:
- Material Selection: High-quality materials such as steel, cast iron, or reinforced plastics are chosen based on the specific application requirements.
- Cutting and Shaping: The raw material is cut and shaped into the basic sprocket form using advanced machining processes.
- Teeth Formation: The teeth are precisely machined to match the specifications of the chain or track with which they will engage.
- Heat Treatment: The sprockets undergo heat treatment to enhance their hardness and durability, making them resistant to wear and tear.
- Finishing: The sprockets are finished with processes such as grinding, polishing, and coating to improve their performance and longevity.
- Quality Control: Each sprocket is inspected and tested to ensure it meets the required standards for strength, precision, and reliability.
This meticulous manufacturing process ensures that our sprockets deliver optimal performance and longevity in demanding applications.